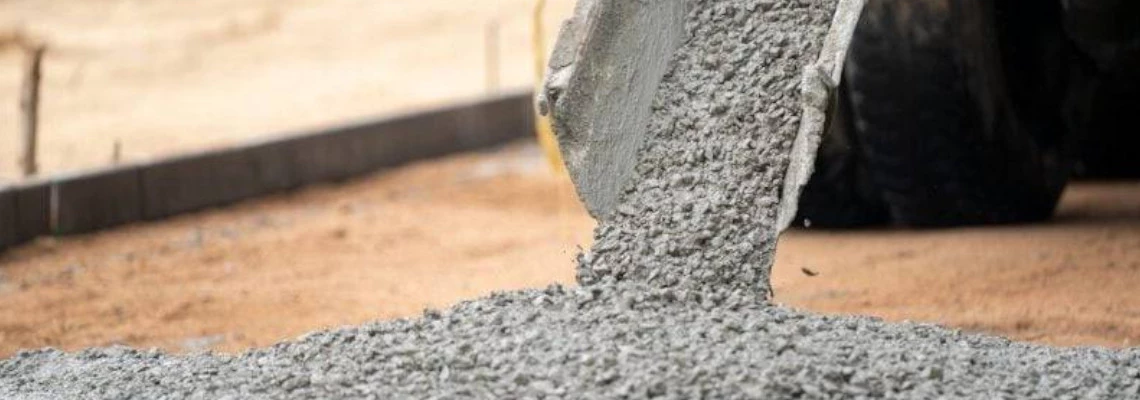
HOW TO REDUCE THE WEIGHT OF CONCRETE?*
Concrete is a fundamental material in construction. It is challenging to imagine pouring foundations, roads, bridges, sidewalks, or buildings without it. Concrete is present on every construction site.
High-strength concrete, in particular, is very heavy, and its density can reach up to 2600kg per cubic metre. This poses many challenges in certain situations, forcing architects to consider alternative forms that would reduce its weight.
In this article, we will explore what can be applied to reduce the weight of concrete, how it affects the overall cost, and whether it is a worthwhile undertaking.
WHAT IS CONCRETE?
The word "concrete" comes from the Latin term "concretus," meaning to grow together.
Concrete is a mixture of cement, water, and aggregates, with variations in characteristics such as density, weight, and strength. The composition of raw materials, type of cement, setting time, and environmental conditions influence these properties.
The concrete mix is not a homogeneous product. It can be moulded into any shape by combining it with water in a state called wet concrete. The concrete curing time is at least 10 hours.
NORMAL WEIGHT CONCRETE
Standard concrete is also known as regular concrete. It is the most common used in the market and readily accessible to the client's usage. It is mostly used in the home environment to undertake construction projects.
In the case of standard concrete, the weight of a 1m3 cube typically falls within the range of 2000 to 2600 kg. That equates to about 20-23 wheelbarrow loads per m3.
This weight range reflects the density and composition variations that can occur in normal concrete mixes. The actual weight within this range depends on factors such as the specific mix design, types of aggregates used, and other components influencing the overall density of the concrete.
LIGHTWEIGHT CONCRETE | HOW IS LIGHTWEIGHT CONCRETE MADE?
This is a lighter version of concrete made from porous aggregates. In the case of lightweight concrete, which includes lighter components such as expanded clay, shale, or slate, its mass can be up to 30% less than that of heavyweight concrete.
Lightweight aggregates can be obtained from natural sources like volcanic pumice, through thermal treatment of raw materials like clay or shale, or by manufacturing from industrial by-products such as fly ash. Processing methods also include utilising industrial by-products like pelletized expanded slab.
Concrete with reduced weight finds applications in the production of items like sound barriers, floor blocks, and other elements demonstrating good thermal insulation properties. It is also used in the construction of load-bearing structural elements such as foundations and floors. Lightweight concrete has a density ranging from 800 to 2000 kg/m³.
Pic. credit:researchgate.net
LIGHTWEIGHT CONCRETE WEIGHT
Lightweight concrete is specifically identified by its weight, which does not surpass 2 tons/m3. This weight threshold serves as the defining criterion for categorising concrete as lightweight. Keeping the density below this limit is crucial in the formulation and production of lightweight concrete, ensuring it possesses the desired characteristics and remains distinct from heavier counterparts.
DOES CONCRETE LOSE WEIGHT AS IT DRIES?
Theoretically, during the initial days, concrete experiences the most significant weight loss. In practice, however, all the water required for concrete formation is absorbed through a chemical reaction, with only a small fraction undergoing evaporation. This water content dictates the amount of weight concrete loses upon drying.
Therefore, there should be minimal difference between the weight when wet and dry. Nevertheless, for safety considerations, it is often asserted that concrete does not decrease in weight after drying.
Concrete acquires its load-bearing capabilities after approximately 14 days and reaches full strength around 28 days.
WHAT CAN I DO TO MAKE CONCRETE LIGHTER?
If reducing the weight of concrete is a priority, EPS (Expanded Polystyrene) fillers can be employed. These fillers, known for their substantial volume and high resistance to compression, help decrease the amount of concrete required. By utilising products like Filcor, it is possible to reduce the weight of concrete by up to 40%. This reduction translates to significant savings in time, money, and reinforcing steel.
Reducing the weight of concrete through the use of EPS fillers also enhances the safety of the structure. The construction becomes overall lighter, thereby increasing safety. An example of such a construction can be seen in concrete stairs, where the application of Filcor polystyrene fillers reduces weight and, consequently, the pressure exerted by the concrete on layers below, such as the concrete floor.
Using more concrete not only adds to its weight but also increases costs for transportation and pouring. By using EPS fillers, these costs can be cut in half, saving on labour, fuel, and time.
Picture credit:cordek.co.uk
Another example of reducing the weight of concrete involves the use of mix design. This innovative method addresses both weight reduction and insulation for concrete floors simultaneously. The approach entails blending small pieces of Styrofoam with the entire mass of concrete. As a result, the concrete not only becomes lighter but also warmer. This is attributed to the manufacturing technology of Styrofoam, which consists of over 90% air, contributing to its insulating properties.
Styrofoam concrete, as it is commonly known, is notable for its remarkably low weight, rendering it suitable for use in floors with low load-bearing capacity. The thermal insulation properties of styroconcrete are impressive, with its thermal conductivity coefficient (lambda) ranging from 0.045 to 0.09 W/m*K, making it up to 10 times better than traditional concrete.
Commonly used beneath panels or for underfloor heating, styroconcrete is a lightweight material employed in floor screeds and ceilings. It serves as a versatile alternative to polystyrene, providing durable insulation with soundproofing benefits, while also offering a levelling and finishing layer.
Styroconcrete is equally effective on roofs, providing insulation for roof pitches up to 30 degrees. Another application is terrace insulation, where its liquid form allows precise filling of gaps, especially in areas with numerous installations.
However, it's crucial to note that while styroconcrete excels in insulation, it's not suitable for supporting structural elements. It should not be used for constructing or insulating load-bearing walls, which carry the weight of the entire structure.
CONCLUSION
Concrete is one of the heaviest construction materials commonly used in daily construction activities. While there are methods to reduce its weight, it's essential to note that these approaches may not always be feasible. The use of EPS fillers is one of the most cost-effective ways to lighten concrete. Additionally, employing Styro concrete represents an innovative method to decrease the lambda value of concrete and reduce its overall mass.
Related articles:
WHAT IS THE NEWEST FUTURE INSULATION?
SMART THERMAL INSULATION THAT'S CHANGING THE GAME
COST-EFFICIENT UK ANTI-HEAVE PROTECTION: TOP 3 NEAR YOU
UNVEILING THE SUPERIORITY OF CELLCORE 225MM HX S: A SHIELD AGAINST SOIL MOVEMENT
WHAT TO CONSIDER WHEN CHOOSING INSULATION MATERIALS
*Insulationgo LTD strives to keep the content accurate and up-to-date, but we cannot be held responsible for any mistakes or exclusions.
The information in this blog isn't expert advice and shouldn't replace talking to the right specialists. Before buying or deciding anything based on this info, it's best to contact the product manufacturer directly to double-check if it's right for what you need.
Descriptions, drawings, photographs, data, proportions, weights, and measured values provided here may change without prior notice and do not establish the guaranteed contractual quality of the products. The recipient of these products holds the responsibility to comply with proprietary rights, existing laws, and legislation.
Using this blog implies acknowledgment and agreement that Insulationgo LTD cannot be held accountable for any damages, losses, or inconveniences resulting from the use or reliance upon the information provided. This limitation of liability extends to all users of the blog, including visitors, readers, and subscribers.