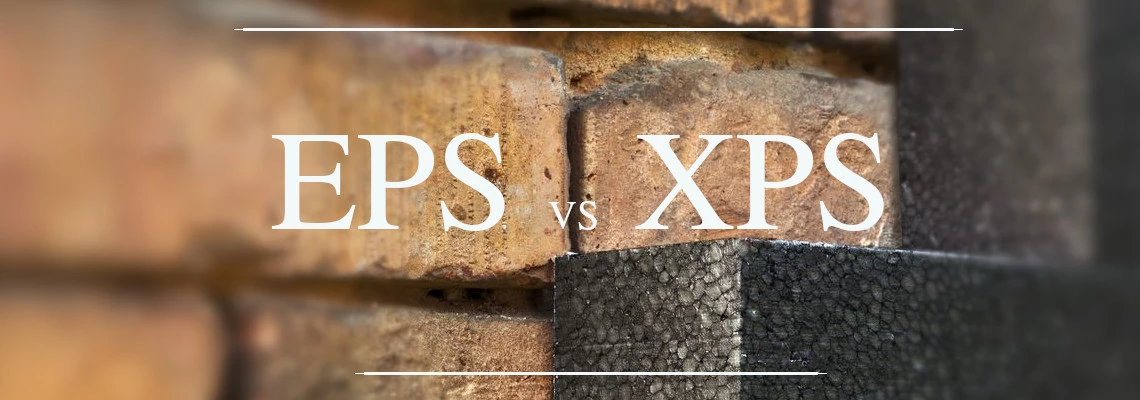
EPS EXPANDED POLYSTYRENE VS XPS EXTRUDED POLYSTYRENE*
Polystyrene is a remarkably effective alternative to other insulation such as PIR. In fact, EPS dominates the European market by 27% in general from other insulating materials as a whole. Today, it is the cheapest method of insulating a building without a doubt. Its popular thickness of 100mm costs only £20.54 per m2. Polystyrene boards are generally recognizable by the colour of the insulation. Boards usually come in two basic colours - white and grey. Fortunately or no, you can also see them in other colours: blue, yellow, pink or green. While white and grey polystyrene is called Expanded Polystyrene (EPS), blue, yellow, pink or green is called Extruded Polystyrene (XPS). So what's the difference, why some are called Expanded, while others Extruded? Moreover, both are polystyrene products and are used for some similar applications, but that is where the similarity stops. Each product has proponents claiming one outperforms the other. So let's clear up all the questions and doubts. In this article you will learn the main differences, why polystyrene comes in different colours, what is its use and most importantly why one is called so, not otherwise. In this blog, we will be discussing the main differences between EPS and XPS insulation.
TABLE OF CONTENTS
- EPS EXPANDED POLYSTYRENE VS XPS EXTRUDED POLYSTYRENE
- IS POLYSTYRENE INSULATION ANY GOOD?
- EPS ABOVE GROUND INSULATION VS XPS UNDERGROUND INSULATION
- TYPES OF POLYSTYRENE INSULATION BOARDS
- EPS EXPANDED POLYSTYRENE – WHITE - GRAPHITE
- EPS EXPANDED POLYSTYRENE PRODUCTION PROCESS
- EPS EXPANDED POLYSTYRENE GRADES
- EPS EXPANDED POLYSTYRENE MANUFACTURERS/PRODUCTS
- XPS EXTRUDED POLYSTYRENE – YELLOW – PINK – BLUE – GREEN
- XPS EXTRUDED POLYSTYRENE PRODUCTION PROCESS
- XPS EXTRUDED POLYSTYRENE MANUFACTURERS/PRODUCTS
IS POLYSTYRENE INSULATION ANY GOOD?
The choice of insulation material plays a critical role in the heat conduction and indoor living quality. Polystyrene sheets are known as the most universal insulation product currently available in the UK market. In fact, polystyrene offers the best cost to performance ratio of any insulation type. With thermal conductivity as low as 0.037W/mK. More importantly, polystyrene boards can help designers achieve the current Building Regulation U-value requirements. The boards are very easy to install and do not require any specialist tools. They come in the form of panels that are installed under roofing and wall cavities or sidings.
This building material is widely used in the building construction industry because it is so versatile. It can be used in wide rage of applications: insulated concrete forms or blocks, structurally insulated panels known as SIP’s and most importantly on Exterior Insulation Systems such as K-Rend.
Polystyrene has many advantages. The big advantage of polystyrene is that it has no thermal drifts or loss of R-Value over the time. There is also no off-casting on site because the blowing agents are trapped inside the polystyrene beads. Since it is impermeable to water, it is mould and mildew resistant. In fact, EPS leads the other insulation products when it comes to R-value per £. This ratio of R-value to the total price of manufacturing and installation per sq. m of material is a crucial component of the process to deliver a budget-friendly, energy-efficient finished home or building. The manufacturing costs of EPS are generally lower compared to other insulating materials like PIR or Phenolic Boards. The EPS board may seem like a simple EWI insulation material but in reality, it is strong and has been used around the globe for decades.
EPS has been proven to remain strong even after decades of use. A report published by EUMEPS in its EPS briefing found that after several strength tests, EPS that had been in the ground for 30 years showed absolutely no loss of strength. Cold flow was also found to be significantly less than expected with long-term exposure to sustained loading. Micro cellular closed cell construction provides EPS with its excellent insulating and shock absorbing characteristics. EPS has very poor water absorption which decreases as density increases.
DISADVANTAGES: contact with hot-water pipes or other surfaces where the temperature is likely to exceed 80 Celsius for continuous periods should be avoided, it can attract termites and ants.
EPS ABOVE GROUND INSULATION VS XPS UNDERGROUND INSULATION
Two of the most frequently installed types of rigid foam insulation are expanded and extruded polystyrene (EPS and XPS). It is key to understand that each product may be more suited for a particular use than the other.
Generally speaking, it is recommended to select the product that will provide the most value for your investment. If you’re installing insulation under a new roof or below slab, XPS can be an effective solution. If your insulation needs are for side wall applications before siding is installed, it is recommended using EPS insulation that not only adds insulation, but also provides durability and lasting support to the siding panel.
EPS vs XPS comparing table
MANUFACTURING
EPS (expanded) and XPS (extruded) are both closed-cell rigid insulation made from the same base polystyrene resins and manufactured differently. During production, EPS’s blowing agent leaves the beads rather quickly creating thousands of tiny cells full of air while XPS’s blowing agent stays embedded in the material for years, thus reducing the capability of air transfer through the material. The closed-cell structure of XPS makes it more resistant to water. Although EPS beads are closed-cell and hydrophobic, they are also surrounded by voids. These voids are responsible for the higher water absorption volume found in finished EPS boards.
THERMAL RESISTANCE
The blowing agent used in EPS is quickly replaced by air and paired with these voids. The result is an EPS insulation product with lower thermal resistance capability when compared to XPS. The air inside the fabric of the EPS conducts heat easily. This is why the thermal conductivity of XPS begins at a lower level than that of EPS. To achieve the same conductivity as that of XPS, higher density or thickness of EPS insulation would be required. XPS will allow heat from passing through its fabric at a slower rate when compared to EPS insulation. EPS manages to pass through 0.11°C for every rise in 1°C in the outdoor temperature while XPS only allows 0.03°C for the same outdoor temperature.
INSTALLATION
XPS has a skin, which makes bonding to that skin less desirable. EPS on the other hand has a surface that accepts bonding very well. Both types of polystyrene can be installed either by powder adhesive or adhesive foam. However, XPS would require adhesive with special additives. EPS foam features a surface that allows for timely and thorough bonding. Alternatively, XPS bonding is much more challenging. Ask anyone who works in the Structural Insulated Panels and Exterior Insulated Finish System industries about these two materials and you will find the overwhelming majority favor EPS’s elite bonding capability. In terms of bonding, EPS is far superior to XPS.
HEAVE PROTECTION
One application where the lower compressive strength of EPS comes in handy is the use in foundations to protect against clay heave. This is where clay soil can expand and contract, causing pressure or ‘heave’ on the foundations which can cause cracking and subsidence. EPS can act like a suspension, contracting when the soil pushes against it and expanding when the soil contracts, thus protecting the foundations from subsidence.
CUSTOMIZABLE
The UK building industry is requiring more customization of products. The 4’ x 8’ sheets are great when you install EPS. This polystyrene is far superior in its ability to make custom sizes, shapes and thicknesses. XPS is limited to certain thicknesses, where EPS can be made up to 1m thick!
WATER RESISTANCE
The difference in water resistance comes down to the fact that XPS has a fully closed cell structure, rather than the partially closed-cell of EPS. Closed-cell insulation means that there are no gaps between the air bubbles, preventing water ingress and permeation. When EPS insulation boards are exposed to moisture, water can accumulate in the spaces between beads. Water affects the R-values of the EPS and the effectiveness of the insulation decreases. Since in XPS, the cells are tightly packed together, water cannot get into its fabric. So they are better at resisting moisture than EPS insulation. They are hence more tolerant of wet conditions.
EPS has a water vapour diffusion resistance of 30-70μ, whereas XPS has a water vapour diffusion resistance of 80-250μ. The water absorption rate by total immersion for XPS is listed at 0.3 percent maximum by volume, compared to 2.0 to 4.0 percent for EPS, depending on product density. That is a substantial difference to be taken into account when specifying a durable project.
FREEZING CONDITIONS
Under freezing conditions, the water present in between the beads can freeze and expand. When this water expands, it breaks the connection between the beads, thus lowering the insulating efficiency even further.
COST
XPS usually beats EPS in every department, except for cost where there is a large difference. This causes them to be out of budget for a lot of people. That means EPS is usually the most cost-effective, budget-friendly choice. EPS is more cost-efficient than XPS, running between 20% – 60%. Contractor will save 40% on a project just switching from XPS to EPS. In fact, EPS with the same level of density is less expensive.
For instance, 50mm EPS would cost you £8.5/m2 while XPS £15.2/m2.
THICKNESSES
When comparing both polystyrenes, XPS is available only in certain thicknesses such as 30mm ǀ 40mm ǀ 50mm ǀ 60mm ǀ 80mm ǀ 100mm.
On the other hand EPS range includes the following readily available product thicknesses: 10mm ǀ 20mm ǀ 25mm ǀ 30mm ǀ 40mm ǀ 50mm ǀ 60mm ǀ 75mm ǀ 90mm ǀ 100mm ǀ 120mm ǀ 140mm ǀ 150mm ǀ 160mm ǀ 200mm.
TIME
Having said that, XPS is more durable and efficient in the long run. Their performance is consistent, and they are least affected by moisture compared to EPS boards.
DRYING
The drying potential for thermal insulation is critical to maintaining thermal resistance (R-value) under severe long term exposure conditions. EPS insulation exhibited drying potential under severe exposure conditions while extruded polystyrene did not exhibit drying potential when exposed to the same conditions. Add in the fact that EPS has drying potential and XPS does not have such potential. Drying potential is particularly important in the context of thermal insulation as it helps ensure the optimal thermal resistance, also known as R-value, is maintained amidst extensive exposure to moisture.
DPC LEVEL
EPS is never as strong as XPS and is more susceptible to crumbling at the edges and to other jobsite damage, which is why EPS is rarely used for walls below DPC level.
COMPRESSIVE STRENGTH
The compressive strength of XPS is greater than the EPS reaching 300-700 kPa. Similar to EPS there is no thermal drift or loss of R-Value over time.
TYPES OF POLYSTYRENE INSULATION BOARDS
Generally speaking, the polystyrene family is divided into two groups: expanded and extruded. While both are polystyrene products and are used for some similar applications, that is where the similarity stops.
EPS EXPANDED POLYSTYRENE – WHITE – GRAPHITE
Either white or graphite EPS70 (Expanded PolyStyrene) is a closed, loose cell construction and thermoplastic foam material made of 98% air and just 2% plastic. The term EPS70 relates to its compressive strength of 70 kPa. The EPS panels are used externally on walls in external thermal insulation composite systems of new buildings and in renovating old ones. A large proportion of this product is also used in the insulating of cavity walls and roof insulation of industrial and domestic buildings. When it comes to the cost, EPS70 typically has the lowest price tag of the tree insulation types PIR, XPS and PUR.
The material is versatile, light in weight, inert, non toxic and made to ensure fungi and bacteria cannot develop on EPS. It is also clean and easy to handle and provides cost-effective solutions to help contractors meet current UK Building Regulations. The product features a Thermal Conductivity of 0.038-0.040W/mK which makes this product a high insulator throughout the year. Although EPS70 has significant resistance to the passage of water vapour, it should not be regarded as a damp proof membrane or vapour-control layer and will not provide a barrier against damp penetration. These EPS insulation boards are available in an extensive range of grades (70,100, 150, 200, 300) and sizes (500mm x 1000mm, 600mm x 1200mm, 2400mm x 1200mm) to suit your requirements. EPS70 insulation boards are available in 14 thicknesses to suit your requirements:
10mm ǀ 20mm ǀ 25mm ǀ 30mm ǀ 40mm ǀ 50mm ǀ 60mm ǀ 75mm ǀ 90mm ǀ 100mm ǀ 120mm ǀ 140mm ǀ 150mm ǀ 160mm ǀ 200mm
Grey EPS is mainly intended for investors who want to achieve the standard of an energy-saving or passive house. The difference between white and grey polystyrene is the presence of graphite, which is added to the expanded polystyrene during the production process. As a result, you get polystyrene with a grey tint, but more importantly - also with increased thermal insulation properties.
White EPS, while still offering a high thermal performance, requires slightly thicker levels to achieve the same thermal performance as graphite-enhanced grey EPS. For example, while a project may call for 120mm of white EPS, the same thermal performance can be achieved with 90mm of grey (graphite) EPS. White EPS is said to be slightly easier to work with when installing external wall insulation systems. This is because white EPS reflects the sun better than grey EPS, meaning it’s not necessary to rasp the insulation, as it will not become as “greasy” when exposed to the sun’s heat.
EPS EXPANDED POLYSTYRENE PRODUCTION PROCESS
EPS insulation material is obtained from expanded polystyrene granules. In the production process, air-filled spheres are created, which are then forced into a mold, where they are formed into a block. In the first stage of production, known as pre-expansion, the expandable polystyrene is exposed to steam and high temperature. This makes the granulate several times larger in volume. It is transported to special silos, where it is seasoned for several hours. Thanks to this, its structure stabilises. In the next stage, the seasoned pearls go to the machine, which again, under the influence of steam and high temperature, forms them into large cuboids, the so-called polystyrene blocks. EPS does not use any CFCS, chlorofluorocarbons or hydrochlorofluorocarbons in the blowing process.
EPS EXPANDED POLYSTYRENE GRADES
When deciding which grade of EPS to use, the density of a block is often the most important factor. The EPS product is classified based on compressive strength and compressive stress.
Compressive strength determines what the grade of EPS is. In fact, it is the maximum uniaxial compressive stress that material can bear before fracturing. Number is assigned to EPS product based on its compressive stress at 10% compression. Generally, the thermal conductivity of EPS core decreases as its density increases.
Wide range of applications comes with a wide range of polystyrene grades available. Industry-wide terms used for differing grades include:
- Low Weight ǀ LD ǀ EPS 50 ǀ Density 50 kPa ǀ Can be used as a cost effective general packaging ǀ Insulation & display ǀ Decorative molding
- Medium ǀ SD ǀ EPS 70 ǀ Density 70 kPa ǀ Can be used in a variety of floor applications both domestic and industrial ǀ Cavity Wall Insulation ǀ External Wall Insulation Systems ǀ EWI boards ǀ Wall and Attic applications ǀ Reinforced render systems
- Heavy ǀ HD ǀ EPS 100 ǀ Density 100 kPa ǀ Can be used as a void former ǀ Fill material ǀ Floor applications ǀ Underfloor heating insulation
- Extra Heavy ǀ EHD ǀ EPS 150 ǀ Density 150 kPa ǀ Can be used as a void former ǀ Floor Pile collars ǀ Column formers ǀ Insulated foundation systems ǀ Concrete floor
- Ultra-Heavy Weight ǀ UHD ǀ EPS 200 ǀ Density 200 kPa ǀ Can be used for insulating garage floor ǀ Flooring under slab ǀ Structural insulated panels (SIPs) ǀ Road and Bridge works ǀ Slope stabilization of mountainous terrain
- Ultra Ultra High Density ǀ UUHD ǀ Density 300 kPa ǀ Can be used in insulated foundation applications with heavy loading such as Embankments back filling ǀ Bridge abutment ǀ Road widening
EPS grades comparing table
EXPANDED POLYSTYRENE MANUFACTURERS/PRODUCTS
- EPS70 ǀ Density 70 kPa ǀ SIZE 2400x1200mm ǀ Jablite, Key-Metzeler, Stylite, Kay-Cel.
- EPS70 ǀ Density 70 kPa ǀ SIZE 500x1000mm ǀ Ceresit, Arbet, Swisspor, Sonalor, Sempre, Neotherm, Yetico, Izotherm, Enerpor, Austrotherm.
- EPS70 ǀ Density 70 kPa ǀ SIZE 600x1200mm ǀ Styrohart, Knauftherm, Stylite.
XPS EXTRUDED POLYSTYRENE – YELLOW – PINK – BLUE – GREEN
XPS (EXtruded PolyStyrene) foam called ‘polyfoam floorboard’ or ‘styrofoam blue board’ is a high cell density, upgrade extrusion skin panel designed especially for floor applications. In fact, the XPS board is a stronger version of polystyrene, being 4 times tougher than a standard EPS70 insulation board. Brands of XPS are generally recognizable by the colour of the insulation. XPS is typically supplied as blue, pink, green or yellow colored boards in 600mmx1250mm, 600mmx1200mm or 615mmx1265mm size.
Blue XPS is made by Styrofoam and Dow Company, green XPS called GreenGuard is made by Kingspan and yellow XPS is made by Soprema. While they are all the same, the colour helps distinguish manufacturing companies on job sites.
XPS board has no thermal drift or loss of R-Value over time. It remains waterproof over the decades. Water simply is not going to seep into the product. Pretty much all XPS floor insulation boards are quite lightweight, so are easy to handle and manipulate on site. Being lightweight, they have low embedded energy and their ozone depleting potential is zero. XPS product is also known as a non-wicking, meaning that there is no water vapour permeance through the damaged areas.
Its excellent compressive strength means it can easily cope with different flooring loads in different grades. Due to its compressive strength, XPS is regularly used in applications where it is going to be under some strain, such as car park decks. It’s also great for use in basements.
XPS boards have a compressive strength of 30 tonnes per square metre, making them a lasting component for underfloor heating installation, below concrete slab, overlay roof or sarking roofs. However, XPS can attract ants and termites even though it is not an organic material. XPS foam insulation is capable of withstanding over 1000 freeze/thaw cycles.
XPS grades comparing table
XPS EXTRUDED POLYSTYRENE PRODUCTION PROCESS
XPS Insulation is manufactured through an extrusion process. XPS insulation begins as polystyrene crystals, which are combined with special additives and a gas blowing agent. The materials are fed into an extruding machine, where they are blended and melted into a thick liquid. The liquid is processed through a die, expanded into foam, shaped, cooled and finally, trimmed. A homogeneous closed cell matrix is produced through the entire cross section of the foam. This matrix of closed cells resists water penetration and that is important because water penetration can reduce R-value if absorbed into the insulation. XPS continues to have a higher R-value at lower mean temperatures even when exposed to water. XPS water potential to absorb is very unlikely to happen. Because it doesn’t absorb water it maintains its insulating power in the presence of water because water can’t get into.
XPS EXTRUDED POLYSTYRENE MANUFACTURERS/PRODUCTS
300 kPa ǀ Flat and pitched roofs ǀ Floors
Manufacturers: KINGSPAN STYROZONE N300R & H350R ǀ EFYOS XPS SL 300 ǀ DOW STYROFOAM FLOORMATE 300 SLA ǀ RAVATHERM XPS X 300 SL ǀ SOPREMA 300 ǀ KINGSPAN GREENGUARD GG300
500 kPa ǀ Retaining Walls ǀ Basement Floors ǀ Car Park Decks ǀ Commercial Floors ǀ Cold Storage Facilities ǀ Swimming Pools ǀ Heavy duty inverted roofs ǀ Load-bearing slabs
Manufacturers: HYTHERM XPS ǀ XTRATHERM XPS 500 ǀ RAVATHERM XPS X 500 SL ǀ SOPREMA XPS 500 ǀ KINGSPAN GREENGUARD GG500 & 500R ǀ POLYFOAM FLOORBOARD SUPER ǀ CELLECTA HEXATHERM XPOOL
700 kPa ǀ Floors ǀ Walls ǀ Roofs ǀ Basements ǀ Swimming pools
Manufacturers: XTRATHERM XPS 700 ǀ SOPREMA XPS 700 ǀ KINGSPAN GREENGUARD GG700 ǀ CELLECTA HEXATHERM XFOOR 700
900 kPa ǀ Heavy weight decks such as reinforced concrete with a ballast layer of gravel or concrete slab
Manufacturers: DOW ETHAFOAM 900
Related articles:
Feel the difference with XPS boards
Filcor lightweight structural fill
*All the information provided in the content published on Insulationgo blog is for informational and educational purposes only. Insulationgo LTD makes every effort to ensure the accuracy and timeliness of the content, but we do not assume any responsibility for any errors or omissions.
The information presented on this blog should not be considered as professional advice or a substitute for consulting relevant experts. Before making any purchase decisions or taking action based on the information presented here, it is strongly recommended to contact the product manufacturer directly to verify the details and ensure its suitability for your specific needs.
By using this blog, you acknowledge and agree that Insulationgo LTD shall not be held liable for any damages, losses, or inconveniences arising from the use or reliance on the information provided herein. This limitation of liability applies to all users of the blog, including but not limited to visitors, readers, and subscribers.