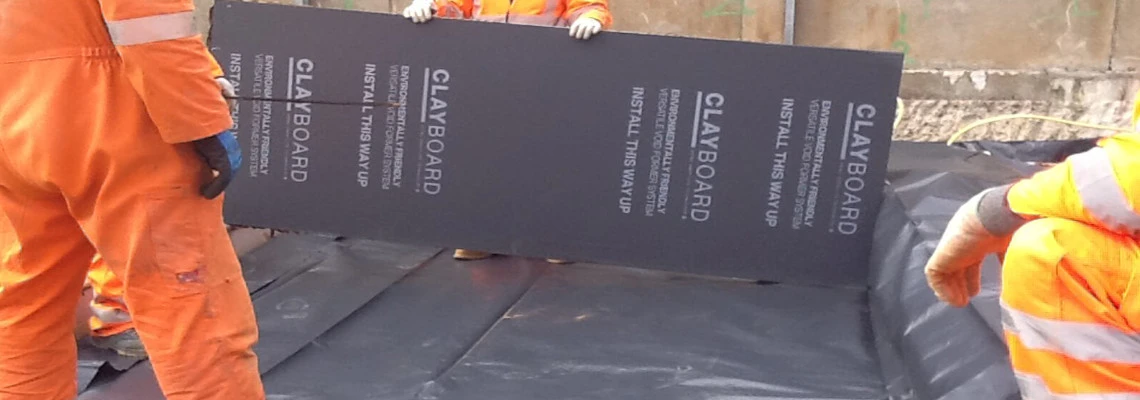
Dufalite Honeycomb Claybord Void Former*
The structural damage caused by clay is well understood by engineers and designer here in the UK. The problem is particularly acute in the South East although climate change is having its effect on soils in other parts of the country.
The solution is to create a space between ground and foundation which soils can expand into.
Clayboard® is strategically designed to prevent structural building damage caused by ground movement. Due to its unique make up, Clayboard creates very little compression and virtually no uplift, allowing for a lighter slab, less reinforcement steel. This void former also reduces soil excavation and muckaway costs. But before that..
How it began?
The story of Dufaylite began way back in 1955 when paper honeycomb technology was first conceived.
Honeycomb shape could offer extraordinary strength and whole world of opportunities.
The first breakthrough came when the honeycomb was used during the Second World War, shortly after that it was found to be a perfect component when placed inside mass produced doors.
From exhibition stands to passive fire protection systems Honeycomb has started journey discovering the next application – Ground Movement Solutions!
The lightweight nature and structural strength of Dufaylite Honeycomb has resulted in it becoming one of the most widely used products in all kinds of applications.
Compressible Polystyrene void former vs Collapsible Dufaylite Clayboard
When pouring the foundation, there needs to be something that can support it while it sets but that will allow the void to actually be formed later on.
Main types of cast- in void formers can be categorised as collapsible or compressible.
Users of products which combat the effects of groundheave are already familiar with the benefits of using the collapsible type, such as Dufaylite Clayboard, over the compressible fill alternatives, made from polystyrene.
Collapsible void formers offer a temporary, sacrificial formwork, which will yield under subsequent heave, allowing soil to move without transferring stresses to the structure.
In the case of Clayboard, this is achieved by “switching off’” its compressive strength after the slab has cured. Compressive strength will collapse under nominal compressive load of approximately 3kN/m².
Compressible, polystyrene void formers, have a much narrower safe load-fail load window and require the designer to significantly thicken the slab in order to resist the uplift.
Polystyrene has to be considerably thicker than Dufaylite Clayboard, so it’s automatically bulkier than collapsible void formers.
Clayboard is 30% smaller than the polystyrene alternatives and requires significantly less ground work to prepare for foundations than the traditional beam and block method.
Moreover, using polystyrene as a void former doesn’t really form voids – polystyrene doesn’t biodegrade, so it’s like landfill under foundations. As a result, it stays underneath the poured concrete and has a much greater chance of exerting force on foundations in the event of ground movement.
However, expanded polystyrene is more commonly used as a void former on construction sites because it is a low cost product. Although polystyrene takes a very long time to biodegrade and is often a common form of pollution in the outdoor environment, particularly polluting shores and waterways.
Dufaylite Clayboard compered to EPS is an environmentally friendly product. It has a biodegradable honeycomb core set between lightweight polypropylene facings.
With Clayboard, the void formed is a true void. With paper honeycomb system, you can form rock solid foundations on dependable voids.
It’s 30% slimmer than polystyrene alternatives and comprises recycled paper and recyclable facings.
The difference is that Clayboard is much thinner, allowing for more boards per lorry to be delivered and means less soil has to be excavated - this keeps down the muck away costs and the ever increasing Landfill Tax duties.
Each square meter of Dufaylite Clayboard can support up to 90 tonnes (90,000kg)
Dufalite innovation
Clayboard® has a 100% recycled and biodegradable paper honeycomb core set between lightweight polypropylene facings which have up to 70% recycled material content.
When dry, Clayboard is rigid and strong enough to support the weight of wet concrete and steel reinforcement without deflection or creep compression. Water is introduced by voidpack pipes to the Clayboard core once the concrete is set. This degrades the honeycomb centre leading to the creation of a void. The board naturally disappear to leave a permanent 100% void with no residual density to pass on heave stresses.
Voidpack pipe simply “switches off" its compressiv strength, taking it from 30kN/m2 down to a nominal 3KN/m2. This ensures that, when the ground heaves, the Clayboard yields with no resistance. The space accommodates clay expansion without exerting undue pressure on the structure above. The resulting void continues to accommodate natural soil shrinkage and expansion to prevent structural damage.
This makes Clayboard an unique product, with its central core designed to collapse under just 3Kn/m² once water has been introduced.
This leaves a true void that is able to account for any ground shift while not introducing more non-biodegradable materials than necessary into the soil beneath a construction. Over time, the paper and water are absorbed naturally back into the soil – a more sustainable solution from start to finish.
Difference between Residencial and Commercial Clayboard
Clayboard® is available in two standard strengths, KN30 (Residential) and KN90 (Commercial)
KN30 has a nominal compressive strength of 30kN/m² when dry and is designed to support the weight of wet concrete up to 1m thick.
KN90 has a nominal compressive strength of 90kN/m² when dry and is recommended for concrete slabs thicker than 1m.
When the core is wetted, both KN30 and KN90 Clayboard® will collapse under nominal compressive load of approximately 3kN/m².
Packaging and delivering Clayboard
Clayboard offers the wet weather protection needed to avoid delays with installing in challenging conditions.
Clayboard® is delivered to site on lightweight pads for easy unloading, and is polythene wrapped for protection.
Clayboard is supplied in sealed units of up to three wrapped boards. The boards will come in a 500-gauge polythene bag, protecting against the elements as well as being resistant to rips and tears in transit.
Deliveries arrive direct to site in a weatherproof seal.
“We are constantly striving to improve and progress our products, making them as efficient for suppliers and contractors as possible.
This new wrapping service enables us to match the weather resistance of plastic alternatives, but continue to provide a unique, sustainable and responsibly produced void former product.”
Ashley Moscrop, Dufaylite’s Group Director said
Clayboard Insallation
Clayboard® panels are safe to handle with no dust and no harmful emissions.
There are three key steps to installing Clayboard:
- preparation
- laying
- forming the void
1. Preparing the site
• On arrival, it’s important the product
remains dry on site at all times.
• Remove all water from the foundation zone.
• Lay a 25mm, flat, dry, level sand blinding
• Lay a polythene sheeting (minimum 500g) onto the blinding
2. Laying the system
• Lay the Clayboard, printed face up, making sure the adjoining panels are positioned up closely together.
• Seal all the joints with Dufaylite Waterproof Tape.
• Lay polythene (minimum 500g) on top of the Clayboard, overlap and tape all joins and leave an overlap at the edges of
the Clayboard.
• Lay steel reinforcement.
• Prepare for later introduction of water by using the Clayboard VOIDPAK System
3. Forming the void
• When the concrete is totally self-supporting, insert hosepipe and introduce a slow flow of water into the Clayboard. Leave water for approximately 2 hours.
• After 24-28 hours, strike through the bottom facing of the Clayboard to allow excess water to drain away. Seal the pipes with cement or waterproof sealant and make good.
Please note the general rule of thumb is a minimum of one Voidpak per 24m2. Where internal beams subdivide the building footprint, then use at least one per enclosed area (more if each enclosed area is >24m2) of Clayboard.
Dufaylite Clayboard Thicknesses
Clayboard® is supplied in panels 2440mm long by 1000mm wide, by the specified thickness. The thickness of product required will be determined by the plasticity index, which is specified by the soil engineer.
Varying thicknesses are available and we’ve shown estimate thicknesses, strengths and requirements below.
*All the information provided in the content published on Insulationgo blog is for informational and educational purposes only. Insulationgo LTD makes every effort to ensure the accuracy and timeliness of the content, but we do not assume any responsibility for any errors or omissions.
The information presented on this blog should not be considered as professional advice or a substitute for consulting relevant experts. Before making any purchase decisions or taking action based on the information presented here, it is strongly recommended to contact the product manufacturer directly to verify the details and ensure its suitability for your specific needs.
By using this blog, you acknowledge and agree that Insulationgo LTD shall not be held liable for any damages, losses, or inconveniences arising from the use or reliance on the information provided herein. This limitation of liability applies to all users of the blog, including but not limited to visitors, readers, and subscribers.