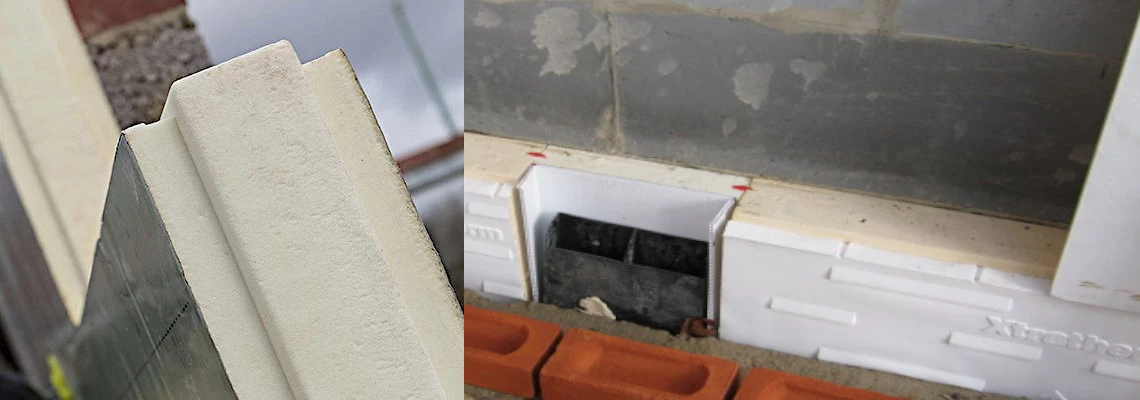
EXPLORING THE BEST CAVITY WALL INSULATION METHODS*
Since the 1980s, cavity wall insulation has been installed in many new homes during construction. Today, cavity wall insulation is a crucial aspect of modern building practices, and it primarily involves filling the gap or cavity between the inner and outer walls of a property with insulation material. Two popular methods of cavity wall insulation are "Full Fill Cavity Insulation" and "Partial Fill Cavity Wall Insulation." In this blog, we will delve into the benefits, drawbacks, and differences between these methods to help you make an informed decision for your property.
Picture credit:labc.co.uk
WHAT IS FULL FILL CAVITY INSULATION?
Full fill cavity insulation is a unique dimension board (450mm/455mm) made from either PIR, Phenolic, EPS or glass mineral wool used to fill the void between outer and inner wall rather than leaving the traditional air gap. In other words, materials shall be considered as full fill cavity insulation where they are designed to be in full contact with both leaves of masonry. When the insulation maintains full contact with the masonry, it effectively creates a continuous thermal barrier, maximising energy efficiency and enhancing the overall insulation effectiveness of the building. The purpose of this design is to ensure optimal thermal performance by eliminating any potential pathways for heat transfer or air infiltration. Some common insulation materials used for full fill cavity insulation include Rockwool, Celotex, Xtratherm (Unilin) or Kingspan. The most common size used as a full fill cavity insulation these days is 115mm, 100mm and 90mm. In any case, the selected product should carry third-party certification confirming its suitability for use in cavity wall applications.
TYPES OF FULL FILL CAVITY INSULATION
Most common types of full fill cavity wall insulation are:
Phenolic core
It is a premium performance insulation with a fibre-free rigid thermoset phenolic core. Kingspan predicts a result of around 0.15-0.17 W/m2K when using 100mm of Kooltherm K106 in a 150mm cavity. However, rigid products are more expensive up front and installation can require more attention to detail on site.
Products:
Kingspan Kooltherm K106 Cavity Board
PIR core
PIR boards are made by mixing chemicals with a blowing agent. This forms large rigid blocks which are low density, closed cell insulation sheets. PIR boards tend to offer the optimum performance vs price ratio as they’re pretty close to phenolic boards when it comes to R-value and yet they’re cheaper. Although you will need a slightly thicker board to achieve the same R-value.
Products:
Xtratherm CT/PIR CavityTherm Thin-R ǀ Recticel Eurowall Plus Cavity Insulation Board
Mineral wool core
Cavity full fill insulation batts are non-combustible and contain water repellent additives which prevent moisture transmission between the outer and inner leaf. Mineral wool cavity insulation is not only waterproof, but lets the walls breathe deterring any unwanted moisture. The batts are simple to install and provide a close fit against brick and blockwork.
Products:
ROCKWOOL® Full Fill Cavity Batts
Superglass Superwall 32 Cavity Wall Batt
Superglass Superwall 36 Cavity Wall Batt
DriTherm 32 Knauf Ultimate Cavity Insulation Slab
DriTherm 34 Knauf Super Cavity Insulation Slab
DriTherm 37 Knauf Standard Cavity Insulation Slab
FULL FILL CAVITY SIZES
All boards are designed to fit between wall ties. Typically they are installed at 900mm horizontal x 450mm. For this reason all boards are made in standard size of 450mm/455mm x1200mm.
Cavity Slabs are available in a range of thicknesses: 50mm, 65mm, 75mm, 85mm, 90mm, 100mm, 115mm, 125mm, 140mm and 150mm.
IS FULL FILL CAVITY INSULATION A GOOD IDEA?
Taking into account the benefits of installing full fill insulation and considering all the advantages of this type of insulation, it can be concluded that full fill insulation is a good idea. Some of the main advantages of full fill cavity insulation include:
-Minimised Drafts
Compared to partial fill insulation, full fill insulation eliminates drafts and air movement within the cavity, creating a more airtight and thermally efficient barrier.
-Elimination of Masonry Errors
With full fill insulation, there is no space left for mortar or cement to fill, preventing the formation of thermal bridges and eliminating the risk of errors in the masonry work.
-Structural Stability
Full fill insulation contributes to the structural stability of the wall by providing additional support and reducing the risk of movement or settling.
-Improved U-Value
The thickness of insulation in full fill cavity walls allows for a higher R-value, indicating better insulation performance and lower heat loss through the walls.
-Noise Reduction
Walls filled with materials like mineral wool provide effective soundproofing, reducing external noise by approximately approx. 40dB.
-Lower Utility Bills
With increased insulation thickness, full fill cavity insulation leads to greater energy efficiency, resulting in reduced heating and cooling costs over time.
WHAT ARE THE DISADVANTAGES OF FULL FILL CAVITY WALL INSULATION?
Full fill cavity wall insulation, like any building method, also has its disadvantages. Some of the main drawbacks include:
-Increased Cost
Full fill cavity wall insulation typically requires more insulation material than partial fill insulation, which can result in higher upfront costs for the materials and installation.
-Installation Challenges
Proper installation of full fill cavity insulation can be more labour-intensive and time-consuming compared to other insulation methods. It requires careful attention to ensure the insulation is evenly distributed throughout the cavity without any gaps or voids.
-Potential for Insulation Settling
If the insulation material used in full fill cavity insulation settles or degrades over time, it can lead to voids or gaps in the insulation layer, reducing its overall effectiveness.
-Risk of Moisture Trapping
In some cases, full fill cavity insulation may increase the risk of moisture trapping if the insulation material used does not allow proper moisture movement and ventilation. This could lead to dampness and mould issues.
-Complexity for Remedial Work
If issues arise in the future and the insulation needs to be removed or replaced, full fill cavity wall insulation can be more challenging to remediate compared to partial fill method.
-Compatibility with Older Buildings
Full fill cavity wall insulation may not be suitable for some older buildings with irregular or narrow cavities, limiting its applicability in retrofitting projects.
-Building Breathability
Some full fill insulation materials may restrict the breathability of the wall, potentially impacting the building's ability to manage moisture vapour.
FULL FILL CAVITY INSULATION BUILDING REGULATIONS
The installation of cavity wall insulation is categorised as notifiable building work under the Building Regulations. This implies that for all buildings that are not exempted from these regulations, it is mandatory to submit a building notice to a building control body, declaring the intent to carry out cavity wall insulation work. This notification ensures that the proposed insulation work complies with the necessary building standards and regulations, and it allows the building control body to oversee and inspect the installation process to ensure it meets safety and quality requirements.
There is an increase in the demand for and the use of full fill cavity wall insulation in the UK. This is due to climate change predictions, the UK government’s commitment to meeting the Kyoto Protocol to reduce greenhouse gases emissions, and the need to conserve energy, supported and driven, at the UK level during the outset of this investigation, by the Code for
Sustainable Homes, Fabric Energy Efficiency Standard, Carbon Compliance and the ever-tightening energy requirements of the relevant national Building Regulations.
In the light of widespread experience of rain penetration in 1989-91, NHBC introduced restrictions on the use of full fill cavity insulation, and similar restrictions were subsequently introduced into Approved Document C to the Building Regulations (England & Wales). At that time the standard cavity width was 50 mm. As energy efficiency standards have improved over the years since, standard cavity widths have increased in order to
accommodate greater thicknesses of thermal insulation, and it is now common to see cavities 100 mm and wider in new homes. Given the increased distance that rainwater would need to travel, it would seem possible that with these wider cavities the potential for rain penetration could be reduced.
INSTALLING FULL FILL CAVITY INSULATION
Full-fill built-in insulation solutions are installed as the walls are built, with slabs being friction-fitted between the inner and outer leaves of the wall and in between wall ties. Where cavity insulation is used mortar joints, including perpends, should be solidly filled with mortar, mortar droppings should be removed from wall ties and the edges of insulation materials. According to NHBC ‘the first row of insulation boards or batts should be supported on wall ties with a minimum of two ties to each board or batt which coincide with horizontal joints in the insulation. Where wall ties need to be closely spaced.’
FULL FILL CAVITY INSTALLATION TIPS
· For cavities up to 100mm, install wall ties in the inner leaf at maximum 900mm horizontal centres and 450mm vertical centres, with additional ties around openings and at corners.
· For cavities greater than 100mm, wall ties should be installed at reduced centres.
· Wall ties must slope down from the inner leaf in order to shed water into the cavity.
· Continue building the inner leaf as you install wall ties, with ties secured by the next row of blockwork.
· Ensure the blockwork structure is kept clean as you build. The faces of masonry must be kept clean and clear of mortar snots and droppings.
· Once the wall ties are secured, the full fill insulation boards can be installed. Wall insulation boards must extend 150mm below the upper edge of floor insulation to prevent thermal bridging at the floor perimeter.
· Boards should be fitted tightly against the leading leaf of masonry supported on the first row of wall ties. The higher side of the rebated edge should always be against the inner leaf.
· Ensure each insulation board is fitted tight against the inner leaf and joints are tightly butted. Each board should be secured by wall ties at a minimum of three points.
· At corner junctions, the rebated edge should be carefully removed with a handsaw or knife to allow a straight butt joint with no gaps. The corner joint should be staggered and the exposed edge of the board should be protected by a vertical DPC of an appropriate width.
Picture credit:self-build.co.uk
WHAT IS PARTIAL FILL CAVITY INSULATION?
Partial fill cavity insulation is a method that involves leaving a 50mm gap between the insulation layer and the outer leaf of a wall. This gap acts as a protective barrier, preventing external moisture from reaching the internal leaf of the wall. It is suitable for buildings of any height.
The primary purpose of the air space in a cavity wall is to act as a barrier against rainwater penetrating the inner face of the wall. For this barrier to be effective, it's crucial that the clear air space is not interrupted by anything other than cavity ties.
PARTIAL FILL MATERIALS
The materials used for partial fill insulation should be of boards, slabs or batts that are sufficiently rigid for ease of handling and to be retained in a vertical position against the inner leaf inside the cavity without sagging or losing shape, so that the edges of the boards remain close butted throughout the useful life of the building. They are supplied at 455mm wide to allow easy installation between standard vertical wall tie spacings and minimum on-site cutting and waste.
Those partial fill materials can be grouped as:
- Inorganic insulants
- Organic insulants
Organic insulants are made from naturally occurring materials that are formed into fibre, powder or cellular structures that have a high void content, as for example, glass fibre, mineral fibre (rockwool), cellular glass beads, vermiculite, calcium silicate and magnesia or as compressed cork. Organic insulants are generally non-combustible, do not support spread of flame, are rot and vermin proof and generally have a higher U-value than inorganic insulants. The organic insulants most used in the fabric of buildings are glass fibre and rockwool in the form of loose fibres, mats and rolls of felted fibres and semi-rigid and rigid boards, batts and slabs of compressed fibres, cellular glass beads fused together as rigid boards, compressed cork boards and vermiculite grains.
Inorganic insulants are based on hydrocarbon polymers in the form of thermnosetting or thermoplastic resins to form structures with a high void content, as for example polystyrene, polyurethane and phenolic. Inorganic insulants generally have a lower U-value than organic insulants, are combustible, support spread of flame more readily than organic insulants and have a comparatively low melting point. The inorganic insulants most used for the fabric of buildings are expanded polystyrene in the form of beads or boards, extruded polystyrene in the form of boards and polyurethane and phenolic foams in the form of preformed boards or spray coatings. With the recent increase in requirements for the insulation of walls it may well be advantageous to use one of the somewhat more expensive inorganic insulants such as XPS (extruded polystyrene), PIR (polyisocyanurate) or PUR (polyurethane) because of their lower U-value, where a 50mm clear air space is to be maintained in the cavity, without greatly increasing the overall width of the cavity.
Partial fill materials used as insulation for the buildings may be also grouped as:
- Expanded Polystyrene
- Phenolic Boards
- PIR Boards
- Mineral Wool Batts.
EXPANDED POLYSTYRENE
Partial Fill Polystyrene Cavity Wall Insulation Boards are a far more cost-effective alternative to PIR that offers a 20% reduction in thickness. This insulation will reduce your carbon footprint and help to decrease heating bills by limiting heat loss. Polystyrene Cavity Wall Insulation Board (EPS 70) (1200 x 450mm - coverage 0.54m²) is manufactured from low lambda polystyrene and is a square edged panel that offers excellent thermal performance when used within masonry wall constructions to satisfy the relevant U-value requirements.
Products:
SPI Stylite Partial Fill EPS
Jablite Partial-Fill Cavity Wall insulation EPS 70 (white) and EPS HP 70 (grey)
PHENOLIC BOARDS
Partial fill cavity board is a premium performance insulation with a fibre-free rigid thermoset phenolic core. It provides a level of performance that is unrivalled in the world of rigid thermoset insulation materials with a thermal conductivity of just 0.018 W/mK across all thicknesses. However, phenolic products are more expensive up front and installation can require more attention to detail on site.
Products:
SR/CW Cavity Wall Insulation Board Xtratherm Safe-R
Kingspan Kooltherm K108 Phenolic Cavity Insulation Board
PIR BOARDS
PIR partial fill cavity boards are a high performance insulation with a fibre-free rigid thermoset polyisocyanurate (PIR) core. They are used to insulate partial fill cavity walls, and have usually have a thermal conductivity of 0.022 W/mK. Rigid products offer better thermal performance allowing you to specify a thinner wall or achieve a better U-value at the same thickness.
Products:
Celotex® CW4000 Cavity PIR Insulation Board
Xtratherm® XT/CW Thin-R Partial Fill Cavity Insulation
MINERAL WOOL BATTS
Mineral wool partial fill batt is designed to provide thermal insulation in partial-fill external masonry cavity walls, with no height restriction (additional requirements apply for buildings above 25 metres in height for partial fill). It can be used regardless of height and in cavities in areas of 'very severe' exposure without rendering the outer leaf. Semi-rigid batts of glass mineral wool or rockwool are the traditional choice. Their flexibility allows them to fit snugly against the masonry as well as knit together at abutments.
Products:
Rockwool® HP Partial Fill Cavity Slab
Knauf Rocksilk® RainScreen Slab
URSA 32 Cavity Wall Insulation Batts
Superglass® Superwall 36
URSA® 32 Cavity Wall Insulation Batts
PARTIAL FILL CAVITY INSTALLATION
Usual practice is to build the inner leaf of the cavity wall first, up to the first horizontal row of wall ties, then place the insulation boards in position against the inner leaf. Then as the outer leaf is built, a batten may be suspended in the cavity air space and raised to the level of the first row of wall ties and the batten is then withdrawn and cleared of droppings. Insulation retaining wall ties arc then bedded across the cavity to tie the leaves and retain the insulation in position and the sequence of operations is repeated at each level of wall ties. Insulation retaining ties are usually standard galvanised steel or stainless steel wall ties to which a plastic disc is clipped to retain the edges of the insulation. The ties may be set in line one over the other at the edges of boards, so that the retaining clips retain the corners of four insulation boards.
IS PARTIAL FILL CAVITY INSULATION A GOOD IDEA?
Taking into consideration the height of buildings where the use of partial fill insulation is allowed, it can be concluded that partial fill insulation is a good idea. In fact, this system is mandated by numerous local authority building control departments, particularly in the UK's various 'exposed' locations. It is suitable for buildings of all heights, unlike full fill insulation, which is approved for use in buildings up to 12m high in any exposure zone.
WHAT ARE THE DISADVANTAGES OF PARTIAL FILL CAVITY WALL INSULATION?
Partial fill cavity wall insulation also comes with certain disadvantages. Some of the main drawbacks include:
-Risk of Thermal Bridging
If the insulation layer is not continuous or there are gaps between insulation materials, thermal bridges can form.
-Moisture Accumulation
If the air gap within the cavity is not correctly ventilated or becomes obstructed, moisture can accumulate within the cavity. This can lead to condensation problems, dampness, and potentially mould growth, which may damage the structure and affect indoor air quality.
-Limited Material Options
Some insulation materials may not be suitable for partial fill cavity wall insulation, restricting the available choices for builders and homeowners. Finding appropriate materials with the necessary thermal and moisture resistance properties can be a consideration.
-Risk of Water Penetration
If the insulation is not appropriately installed or if there are gaps or voids, water may penetrate the cavity during heavy rainfall or driving rain, potentially compromising the insulation's effectiveness and leading to moisture-related issues.
FILLING WALL CAVITY WITH INSULATION / BEST CAVITY INSULATION
Houses constructed before 1920 typically feature a single-skin brick wall, which means there is no cavity to be filled. Consequently, these types of homes can only be treated with external or internal wall insulation.
Properties built after 1920, on the other hand, have a cavity wall, allowing for the installation of cavity wall insulation.
The best materials for filling your cavity wall are:
Cavity insulation for new walls - this gap can be filled with insulation material while the walls are being built. It typically involves using products such as Xtratherm CT/PIR (full fill) or Xtratherm XT/CW (partial fill).
Polyurethane foam insulation is widely used for new walls and is regarded as the most effective thermal cavity wall insulation available. Its exceptional insulating properties make it an excellent choice for improving a building's energy efficiency. However, the installation process can be complex and requires precise application to ensure optimal performance.
Due to the intricacies involved, it is highly recommended to enlist the expertise of a professional insulation installer. They possess the necessary knowledge and experience to handle the installation correctly, avoiding any potential issues or mistakes that could compromise the insulation's effectiveness.
Picture credit:self-build.co.uk
Mineral wool - among the various options for cavity wall insulation, mineral wool stands out as a popular and widely used choice. One of its key advantages is the versatility it offers during installation. The ability to place it between the studs in various configurations makes it a preferred option for many builders.
Mineral wool insulation can be effortlessly slid between the joists, allowing for a seamless fit within the cavities. It also boasts the advantage of being easily packed tightly, ensuring an effective and snug insulation layer. Additionally, it can be conveniently pre-cut to match different joist widths, streamlining the installation process and saving valuable time on the job.
With its adaptability and straightforward installation, mineral wool remains a top pick for cavity wall insulation, providing reliable thermal performance and contributing to energy-efficient buildings. Picture credit:en.wikipedia.org
Blown mineral wool
Mineral wool can be blown into a property’s cavity walls to form an energy efficient insulating layer.This type of insulation material is used to fill cavities or spaces in buildings. It is made from natural minerals, typically rock, which are melted and spun into fine fibres.
The resulting wool-like material is then blown into the desired areas using special equipment.
Blown mineral wool provides excellent thermal and acoustic insulation properties, helping to improve the energy efficiency and soundproofing of a building. It is particularly useful for filling hard-to-reach or irregularly shaped spaces, providing a seamless and effective insulation solution. Picture credit:rockwool.co.uk
Polystyrene beads
Polystyrene beads are small, lightweight, and spherical particles made from expanded polystyrene (EPS). These beads are used as an insulation material, especially in cavity walls and other spaces that require filling. The beads can be injected into the cavities, where they fill the voids and create a thermal barrier.
Polystyrene beads are known for their excellent insulation properties, providing resistance to heat flow and helping to maintain a comfortable indoor temperature.
Additionally, they are moisture-resistant and can contribute to reducing energy consumption and lowering heating and cooling costs in buildings.
Picture credit:ecobead.com.au
FULL FILL VS. PARTIAL FILL INSULATION
-Full-fill insulation can be slightly quicker to fit, as there’s less need to focus on how the material is held in place.
-It will also offer slightly better thermal performance over partial-fill for the same wall thickness. Put simply, with a 150mm cavity you’ll be able to include a full 150mm thickness of insulation; which is likely to net you a U-value of around 0.20 W/m2K on a typical brick and block setup when using a product such as Superwall 36 slab from Superglass.
-Partial fill cavity insulation may not provide as high a level of thermal efficiency compared to full fill cavity insulation. The presence of gaps and voids in the insulation can allow heat to escape more easily, leading to potential energy loss and decreased indoor comfort.
-Partial fill- the 50mm gap has the advantage over full fill cavity insulation of reducing the chance of any moisture that does penetrate the outer leaf bridging through to the internal structure.
WHAT IS THE BEST CAVITY WALL INSULATION METHOD?
The best cavity wall insulation method will depend on the specific needs of the building, regional climate conditions, and budget considerations. Full fill insulation is often favoured for new constructions where thermal performance is a primary concern and where the cavity width is consistent and easily accessible. Partial fill insulation, on the other hand, can be more suitable for existing buildings or constructions with narrower cavities, where the air gap can help with moisture control and where installation access might be more challenging.
CONCLUSION
In conclusion, when it comes to cavity wall insulation, there are several effective methods to choose from, each with its advantages and considerations. Full fill cavity wall insulation offers superior thermal performance and can be ideal for new constructions with consistent cavity widths. On the other hand, partial fill cavity wall insulation provides satisfactory energy efficiency and moisture control, making it a viable option for existing buildings or constructions with narrower cavities.
Related articles:
MASTERING HOME INSULATION: UNLOCKING COMFORT, ENERGY EFFICIENCY, AND SAVINGS
PARTIAL FILL CAVITY INSULATION
FULL FILL CAVITY INSULATION AS WE KNOW IT
Bibliography
1.www.nhbc-standards.co.uk, Superstructure excluding roofs, ‘External masonry walls’, accessed 22 July 2023
Pictures credit:
*All the information provided in the content published on Insulationgo blog is for informational and educational purposes only. Insulationgo LTD makes every effort to ensure the accuracy and timeliness of the content, but we do not assume any responsibility for any errors or omissions.
The information presented on this blog should not be considered as professional advice or a substitute for consulting relevant experts. Before making any purchase decisions or taking action based on the information presented here, it is strongly recommended to contact the product manufacturer directly to verify the details and ensure its suitability for your specific needs.
By using this blog, you acknowledge and agree that Insulationgo LTD shall not be held liable for any damages, losses, or inconveniences arising from the use or reliance on the information provided herein. This limitation of liability applies to all users of the blog, including but not limited to visitors, readers, and subscribers.