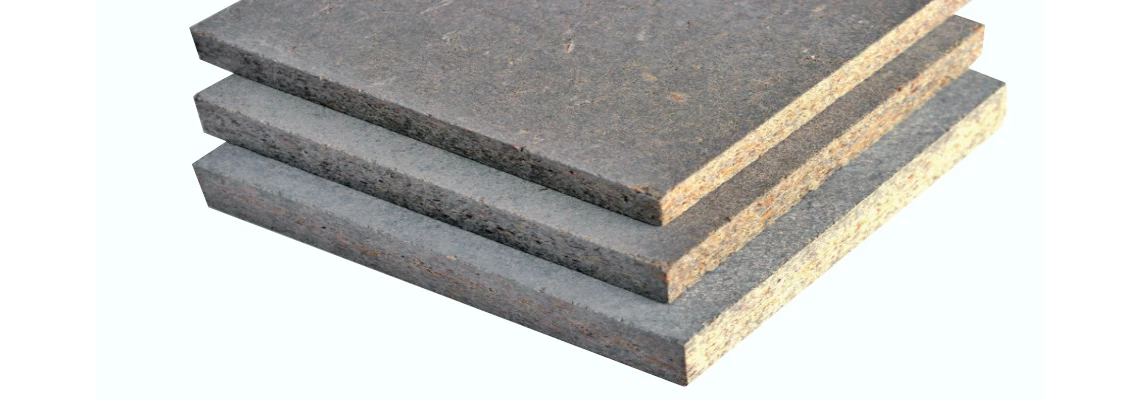
✔Reading time: 915sec✔
CEMENT BONDED PARTICLE BOARD*
In recent years cement bonded particle boards have become important material for building constructions. No wonder why. Boards belong to the modern composite building materials generation that can last 50 years. These materials combine strength and durability of cement with simplicity of wood processing and flexibility.
Thanks to its physical and mechanical characteristics, the product is considered one of the best materials for lightweight constructions. Further in this article, you can find all relevant information about Cement Bonded Particle Board.
TABLE OF CONTENTS
- CEMENT BONDED PARTICLE BOARD
- WHAT IS CEMENT BONDED PARTICLE BOARD?
- CEMENT BONDED PARTICLE BOARD MANUFACTURING PROCESS?
- CEMENT BONDED PARTICLE BOARD FINISH
- DIFFERENCE BETWEEN STANDARD PARICLEBOARD AND CEMENT BONDED PARTICLE BOARD?
- CEMENT BONDED PARTICLE BOARD THICKNESS/SIZE
- CEMENT BONDED PARTICLE BOARD USES
- CEMENT BONDED PARTICLE BOARD PRODUCTS
- CEMENT BONDED PARTICLE BOARD DENSITY
- CEMENT BONDED PARTICLE BOARD REACTION TO FIRE
- CEMENT BONDED PARTICLE BOARD REACTION TO WATER
- CEMENT BONDED PARTICLE BOARD REACTION TO NOISE
- CEMENT BONDED PARTICLE BOARD BUILDING REGULATIONS
- CEMENT BONDED PARTICLE BOARD FLOORING
- CEMENT BONDED PARTICLE BOARD EXTERNAL CLADDING
- CEMENT BONDED PARTICLE BOARD PRICE
- CEMENT BONDED PARTICLE BOARD CUTTING
- CEMENT BONDED PARTICLE BOARD INSTALLATION
- CEMENT BONDED PARTICLE BOARD FIXINGS
- CEMENT BONDED PARTICLE BOARD DECORATION
WHAT IS CEMENT BONDED PARTICLE BOARD?
Picture credit:eboss.co.nz
Cement bonded particle board goes by many names such as CBPB, CP boards, Cem panels, cement impregnated chipboard or sheathing board.
Cement bonded particle board (CBPB) is a revolutionary composite rectangle shape material made of Portland cement (65%), shavings-sawdust, dry pine debarked wood particles/spruce chips (24%), mineralisation materials (2.5%) and water (8.5%).
The first impression of the panel is that it is grey in colour typical of cement, has a smooth almost polished surface and is heavy. Board is suitable for both internal and external applications such as wall partitions, floors, ceilings, general lining and acoustics. Product is free of formaldehyde and asbestos and its surface is comparable to smooth cobblestone.
Pic credit:amroc.de
Advantages: the CBP boards have very interesting properties regarding stiffness, fire, acoustics and resistance to termites and microorganisms, cheaper and more environmentally friendly production techniques.
Disadvantages: weight per square foot which is quite high and makes its handling by one person difficult.
CEMENT BONDED PARTICLE BOARD MANUFACTURING PROCESS?
Cement-bonded particleboard (CBPB) was first commercially manufactured in the early 1970s and has continued to be manufactured till now. As a curiosity, over 55,000 m3 of these boards are produced annually in the Czech Republic.
There are mainly two different methods in use to produce CBPB; the Hatscheck process and the Elmendorf process. According to Scientific research - an academic publisher:
The Hatscheck Process
A drum rotates in a water based slurry of fibres and mineral materials, including Portland cement. The drum feeds a film of slurry onto a felt while simultaneously partially pressing the water from the film, upon which the felt moves the film onto a forming roller where a sheet of desired thickness is built up by a number of turns. Subsequently, the stack of films is removed from the roller and laid out flat to form the sheet.
The Elmendorf Process
Fibres, water and then cement are thoroughly mixed, with the mix typically made with fibres amounting about 70% of the volume; with the ratio by weight: cement 60%, wood 20%, water 20%. The damp matrix is fed continuously onto a bottom (caul) plate to form a mat. The caul plates with mats are stack-pressed to yield boards of desired thickness. Under the pressure, of 1.5 - 3.0 MPa, water squeezes out of the wood particles and combines with the cement to form a paste. The stack of boards is clamped together at this pressure and moved to a curing cabinet, with controlled humidity and temperature (70˚C - 80˚C) and left there for curing for 8 - 20 hours.
CEMENT BONDED PARTICLE BOARD FINISH
Board comes from FSC controlled forests with reforestation cycles. Depending on the chosen finish, wood particles can be visible on the surface of the board, enhancing its natural appeal. This means the board may present some shades due to the composition of cement porosity and salts. Usually these shades run in lengthways, the directions as a result of the production line up. To polish the panel surface it’s recommended to use a sanding disk of 180gr minimum. This procedure will remove the superficial cement salts and will homogenise the panel surface, smoothing out the natural shades. When the board is sanded, wood particles become visible on the board surface, enhancing the board’s natural appeal.
The cement bonded particle board can be later on painted for decorative purposes with a large variety of paints.
WHAT IS THE DIFFERENCE BETWEEN STANDARD PARICLEBOARD AND CEMENT BONDED PARTICLE BOARD?
As general, in relation to standard particleboard, there is one main difference with cement bonded particleboard. The finished and installed cement bonded boards do not release pollutants into the environment over time.
Consequently the board offers a more environmental friendly alternative to particleboards glued with formaldehyde. Moreover, the proportion of wood as a raw material is lower than in conventional particleboard. Same fastening methods are used for wooden particle boards and cement bonded particle boards.
CEMENT BONDED PARTICLE BOARD THICKNESS/SIZE
CBP boards can be manufactured in 6mm up to 40mm. The sizes of cement bonded particle boards shall be as follows:
Length:
1200mm x 2400mm | 1260 x 2600mm | 1260 x 3000mm
The most common manufactured board is 4" x 8"
Width:
600mm | 1200mm | 1250mm
Thickness :
6mm | 8mm | 10mm | 12mm | 16mm | 19mm | 22mm | 25mm | 28mm | 32mm | 40mm.
The panels can also be supplied with custom dimensions for specific quantities to be established directly with our Sales Office.
CEMENT BONDED PARTICLE BOARD USES
Cement bonded particle board is suitable for multiple uses such as:
- floors,
- self-supporting dry screeds,
- partition walls for offices,
- radiant floors,
- exhibition stands,
- stiffening structures,
- high resistance external and internal coatings,
- sheathing panel for steel frame systems,
- sheathing panel for external wall insulation,
- fire doors,
- naval fittings.
Picture credit:eltomation.com
Cement bonded particleboard has been used in almost every conceivable form of commercial, residential and public sector building type, including:
- Hotels,
- Leisure Centres,
- Prefabricated Houses,
- Office Buildings,
- Schools,
- Hospitals,
- Apartment Blocks,
- Industrial Premises,
- Sporting Arenas,
- Student Accommodation.
CEMENT BONDED PARTICLE BOARD PRODUCTS
Cement Particle Board may differ in characteristics depending on the manufacturer. Most commonly used cement bonded particle boards are:
- Euroform versapanel cement bonded particle board
- RCM Cemboard cement bonded particle board
- Cembrit Cempanel
- Betonwood cement bonded particle board
- JCW acoustic cement particle board
- Viroc cement bonded particle board
- StoneREX cement bonded particle board
- AMROC cement bonded particle board
- Magboard cement bonded particle board
CEMENT BONDED PARTICLE BOARD DENSITY
Cement bonded particle board density ranges from 1350 up to 1480 Kg/m³ depending of the manufacturer. Its compression strenght is usually no less than 9000 kPa. To put this into perspective, brick has a compression strength of 8000 kPa. Cement bonded particle board is therefore used in flooring and as roof support.
Board also has a bending strength more than 10.5 N/mm2. That describes its ability to resist deformation under load. The 10.5 N/mm2 figure enables it to be used as a resistant structural element.
Weight per sheet (2400mmx1200mm):
- 10mm - 42.62 kg
- 12mm - 51.15 kg
- 16mm - 68.20 kg
- 18mm - 76.72 kg
- 22mm - 82.36 kg
- 24mm - 89.85 kg
- 28mm - 104.83 kg
- 36mm - 134.78 kg
- 40mm - 149.76 kg
Please note that most manufacturers produce cement particle boards with a minimum density of 1350 kg/m3. This means that a 2400mm × 1200mm × 12mm panel will weigh approximately 51kg. This can give rise to handling problems, especially with thicker panels.
CEMENT BONDED PARTICLE BOARD REACTION TO FIRE
As a single board material Cement Particle Board is probably one of the most versatile sheet materials available when it comes to application in areas which have to be fire rated. Cement bonded particle boards offer a B1 fire rating, according to European standards, making it the ideal facade for a variety of structures where safety is paramount.(Reaction to Fire: EN 13501-1 A2-s1,d0)
Pyrok can be sprayed directly onto cement bonded particle board to increase the fire protection properties of cement bonded particle board.
CEMENT BONDED PARTICLE BOARD REACTION TO WATER
Cement bonded particle boards are resistant to atmospheric agents, because the wood fibers are protected from the cement against external damage. Please note, cement bonded particle board is not actually waterproof, but it is highly resistant to absorbing moisture and has excellent drying properties. While they are water resistant and unaffected by water exposure, this is for limited periods of time only – typically 3 to 6 months exposed externally, but it varies from product to product.
It is not subject to weather influences. Under the action of water it does not disaggregate.
The value of the water vapour resistance factor (µ) for CBPB varies with the method of determination(BS EN ISO 12572) as set out below which is an extract from BS EN 12524 and BS EN 13986.
- wet 30 µ-0.03mm
- dry 50 µ-0.05mm
When the cement bonded particle board is tested according to the standard MSZ EN 317 the thickness swells of 1,5% after a soak of 24 hours.
It can be asserted that initially the water absorption increases drastically and reaches a µmax value after about 50 hours of soaking. There should be no significant changes in the moisture content after this period of soaking. The average µmax value is 27%. As a guide, CBPB can be expected to attain the moisture content under specified conditions in table below
CEMENT BONDED PARTICLE BOARD REACTION TO NOISE
The cement bonded particle boards have the intrinsic characteristics that make itself suitable to be an excellent sound insulation. Its consistent mass promotes the abatement of high frequencies and its heterogeneous composition contributes greatly to increase the sound insulation.
The acoustic abatement coefficient is equal to 31 dB for single board with 12 mm of thickness with a coincidence frequency of 4200.
Cement Particle boards are great when helping reduce transmission and airborne sound due to the density of the combined cement and chipboard bond. In fact, cement bonded particle boards will improve the overall acoustic performance based on the board's mass content.
- 8 mm-29 dB
- 10 mm-31 dB
- 12 mm-32 dB
- 16 mm-33 dB
- 18 mm-33 dB
- 20 mm-33 dB
- 24 mm-35 dB
CEMENT BONDED PARTICLE BOARD BUILDING REGULATIONS
CBPB manufactured in Europe must now be specified in accordance with BS EN 634-1 Cement-bonded particle boards.
Specification. General requirements1.As explained in PanelGuide Section 2,
CBPB that is used in construction must comply (by law) with the Construction Products Regulation (CPR) by compliance with BS EN 13986; this standard calls up BS EN 634
which is in two parts:
• BS EN 634-1 Cement-bonded particle boards.
Specification. General requirements
• BS EN 634-2 Cement-bonded particleboards.
Specification.
CEMENT BONDED PARTICLE BOARD FLOORING
Cement bonded particle board has been used worldwide in a number of different flooring applications such as acoustic performance, rot resistance or strengthening of construction.
Cement bonded particle boards offer excellent acoustic performance, therefore are especially great for acoustic flooring.
The minimum thickness of cement bonded particle board used on the floor is either 18mm for joist centres up to 500mm or at least 22mm for centres up to 600mm. However, 18mm size is most commonly found to be used in the UK. For CBP board widths, you are generally going to find sizes of 600mm and 1200mm. The boards themselves are 4-5 times as wide as a standard timber floorboard, so this makes them much easier to fit and you can cover a larger area much quicker. Lengths can range between 2.4m all the way up to 3m.
As a general rule, the thickness of the CBP board you need will depend largely on joists span.
You will cement bonded particle boards in builder’s merchants and timber yards. Please note, if you visit somewhere like Wickes or B&Q, everything will be in metric (mm). Essentially, if you want to save money you can buy from us.
Cement bonded particle board comes in tongue and groove or square edge finish. While tongue and groove joints are commonly used for flooring applications, square edge boards are commonly used on walls.
T&G CBP boards are relatively quick to lay on the floor. The tongue and groove edges make a strong bond between the boards. Cement bonded particle boards are laid lengthways across the joists and ‘printed side’ up. Provided you don’t anticipate having to lift the flooring again, you should glue the joints to make them even stronger.
CEMENT BONDED PARTICLE BOARD EXTERNAL CLADDING
Cement particle board is also superior when used as internal linings on rainscreen cladding projects (eaves, roof overhang).
Cement bonded particle board can be covered for outdoor use, with ceramic or stone tiles that can be easily installed directly on the surface of our panels. Its structural stability makes an ideal carrier board for insulated render as well as for large or small format coated cladding systems.
Where CBP board is used as a carrier board for external cladding applications particular attention should be paid to wind load. A 5mm gap should be left between boards which is covered with a 50mm, 1436 grade aluminium sealing tape, alternatively the gap can be filled with a bead of polyurethane sealant.
Sealing tape
If sheathing is left exposed for any length of time designers should take account of wind load below. Otherwise sheet and fixing centres are 600mm regardless of thickness.
CEMENT BONDED PARTICLE BOARD PRICE
Cement bonded particle board offers a long performance life at a cost effective price. We stock a wide range of Cement Particle Boards in the most used thicknesses such as 10mm,16mm, 18mm, 22mm depending on your price point and specifications. As a guidance you should expect to pay:
- £ 56 ex VAT for 10mm thick board (2.88m2)
- £ 64 ex VAT for 12mm thick board (2.88m2)
- £ 163 ex VAT for 18mm thick board (2.88m2)
- £ 213 ex VAT for 22mm thick board (2.88m2)
CEMENT BONDED PARTICLE BOARD CUTTING
The tools used for comment bonded particle boards are identical to those used with wood. For thicknesses up to 19mm, circular saws are ideal. Preferable cutting tools are the ones with electronic speed control.
For greater thicknesses such as 22mm or 24mm, the support of a workbench is recommended to support safety requirements as well as ensuring even surface quality.
A jigsaw is ideal for curved cuts. On the other hand a conventional hammer drill is ideal for drilling into the board.
Using a router, the edges of the panel can be machined to form bevel, tongue-groove or half lap joints. When cutting, effective emission ventilation should be in place. The use of high speed cutting tools should be avoided unless dust extraction is in place.
CIRCULAR SAW
When working with hand-held circular saws, a setting between 3,000-4,000 RPM should be used. The blade diameter should be between 250-400mm. The tooth count depends on the panel thickness:
- for panel thicknesses up to 12mm: 48-72 teeth
- for panel thicknesses in excess of 12mm: 36-60 teeth
CEMENT BONDED PARTICLE BOARD INSTALLATION
The boards shall not crack or split when drilled, sawed or nailed. Cement bonded particle building boards can be fastened to load-bearing structures using screws, metal dowels, nails or rivets. It is recommended that cement bonded particle board is installed in brick bond fashion as per the diagram.
CEMENT BONDED PARTICLE BOARD FIXINGS
It is not recommended to fix sheets onto a structure using screws for gypsum boards.
For installation of cement bonded particle board with a thickness of 10-24 mm to vertical, horizontal structures (floors, partitions, ceilings) it is advised to use special fasteners to connect them together.
The table below shows the minimum dimensions of screws for fixing cement-bonded particle boards to the elements of load bearing frames, depending on its' thickness and the diameter of concrete dowel.
SCREWS
Countersunk parallel core screws should be used in both edge and face fixings because they have greater holding power than conventional wood screws. A high ratio of overall diameter to core diameter is desirable. Because of the high alkalinity of the panel, stainless steel or galvanised screws with a diameter up to 4.2mm should be used.
NAILS
Manual nailing of serrated or twisted nails up to 3.1mm in diameter is possible in panels up to 12mm in thickness.Above 12mm, either pre-drilled manual insertion or nonpre-drilled pneumatic fixing should be used. Nails must be flat-headed and galvanised, sheradised or of stainless steel.
STAPLES
Stapling is a very economic fastening method. It is used as a permanent form of attachment with the help of power or compressed-air tools, especially in the industrial sector. It is important to ensure that the staples are driven into the panel edge at a 30° angle. Resin coated staples have proven to be particularly effective. In accordance with DIN 1052, the staples should have a wire diameter of dn ≥ 1.8mm. The recommended thickness range of the panels for stapling is 10 - 20mm.
STEEL FRAME FIXINGS
TIMBER FRAME FIXINGS
The use of a cordless nail gun enables the rapid fixing of cement bonded particle board to timber frame or battens. ITW Paslode nails, 2.8mm diameter x 50mm length are recommended for timber frames. You should ensure that the nail head is flush to the face of the panel.
CEMENT BONDED PARTICLE BOARD DECORATION
Cement bonded particle board is a wood based material. Applying a paint coat on-site is generally possible. In fact, a properly applied paint coat reduces the swelling characteristics by containing the moisture absorption.
Prior to applying the paint, the cement bonded particle boards must be prevented from absorbing moisture by observing proper storage and processing procedures. If this is not done, easily water soluble constituents of the cured cement can leach to the surface with the subsequent evaporation of moisture as calcium carbonate, resulting in paint damage.
Painting should be done when the board is completely dry and atmospheric humidity is dry.
Bibliography:
violent.ee/userfiles/files/CSP%20katalog-ENG.pdf
wpif.org.uk/uploads/PanelGuide/PanelGuide_2014_Annex2C.pdf
ncbi.nlm.nih.gov/pmc/articles/PMC8619079/
betonradiant.com/pdf/Catalogue-cement-bonded-particle-board-BetonWood.pdf
Related articles:
Vapour control layer. Dark side
How to install insulated plasterboard
*All the information provided in the content published on Insulationgo blog is for informational and educational purposes only. Insulationgo LTD makes every effort to ensure the accuracy and timeliness of the content, but we do not assume any responsibility for any errors or omissions.
The information presented on this blog should not be considered as professional advice or a substitute for consulting relevant experts. Before making any purchase decisions or taking action based on the information presented here, it is strongly recommended to contact the product manufacturer directly to verify the details and ensure its suitability for your specific needs.
By using this blog, you acknowledge and agree that Insulationgo LTD shall not be held liable for any damages, losses, or inconveniences arising from the use or reliance on the information provided herein. This limitation of liability applies to all users of the blog, including but not limited to visitors, readers, and subscribers.