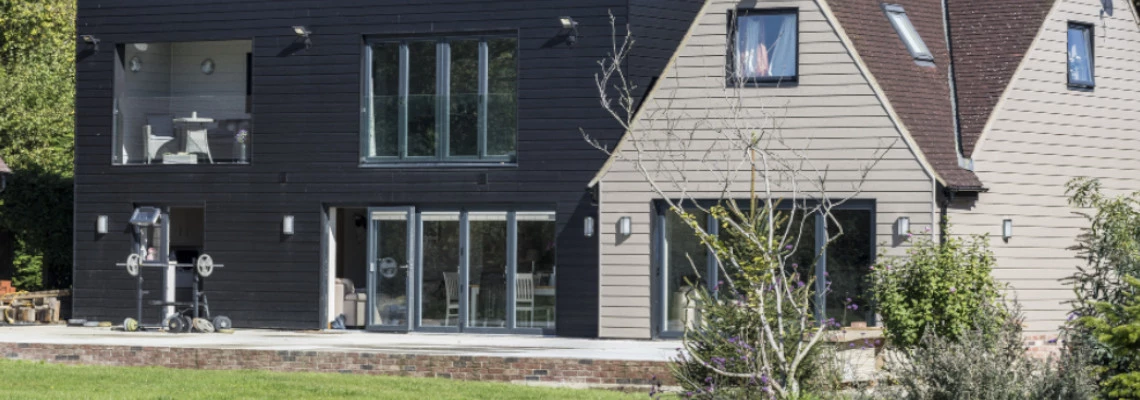
Fibre cement technology*
A house is built to last. That’s why cladding products should stay as beautiful, strong and weather resistant as they were when first applied. Fibre cement cladding is a product which affixes to the exterior of a house or other structure. It masquerades as masonry or wood, experiences wear-and-tear like concrete and can help your home to survive some of the harshest elements of your local environment. Manufacturers create this item by mixing Portland cement with wood pulp so that you can improve the affordability, durability and looks of your property.
Fibre cement siding comes with many durability advantages when compared to the other materials which are available in today’s market.
Fibre cement construction materials have been around for over 100 years. The superior characteristics of fibre cement cladding products make them the preferred, low maintenance choice of professional builders, architects and homeowners alike. Boards are thinner and stronger then most alterative building materials. "What makes this board so strong and flexible" is another question here. What they are exactly made of?
The DNA of fibre cement cladding
The manufacture of fibre cement involves using both organic and inorganic raw materials. The inorganic can include:
- Portland cement
- Water
- Silica
- Silica fume
- Limestone flour
- Meta kaolin
- Fly ash
- Calcium silicate
The organic components can include:
- Cellulose pulp (Kraft)
- Recycled fibers
- Synthetic fibers
- Flocculants
- Defoamers
The major components involve cement, water, silica, limestone flour and fibers. The others mentioned are used in minor quantities.
Main components used for fibre cement board
Fibre cement technology - Hatscheck process
The most popular technology used in fiber-cement manufacturing is the Hatschek process dating back to 1890. It is named after its developer Ludwig Hatschek of Austria who based it on the pulp and paper manufacturing process.
He simply combined slurry with cellulose, reinforcing fibers and Portland cement in water. This fed into a paper making machine in which a cylindrical sieve or sieves rotate through the slurry. The solids are deposited on the sieve which on each rotation transfers the layer of solids onto a continuous belt. The layers are built up to the desired thickness and then removed and if necessary compressed by stack pressing.
Ludwig Hatschek
source:http://www.edubilla.com/inventor/ludwig-hatschek/ https://mfl-fc.at/en/company/history.html
Fibre cement production process
Silica sand with the particle size between a quarter to half mm (similar to beach sand) is loaded onto an underground conveyor outside the manufacturing plant. The conveyor takes the sand to ball mill where it is ground out to a fine powder.
Sand transported
source:https://www.youtube.com/watch?v=lpS6zhsLhmc
Then steel balls tumble around with the sand in revolving cylindrical grinder.
Steel balls used in manufacturing process
source:https://www.youtube.com/watch?v=lpS6zhsLhmc
In order to reduce the amount of dust created and to help move the powder to the next stage, water is pumped in.
Water added to sand
source:https://www.youtube.com/watch?v=lpS6zhsLhmc
Then the sandy liquid is drained in the tank until the solid particles make up about 80% of the volume. Next wood pulp is added to the mix.
It is the wood pulp that gives fibre cement its bending strength. Without it the product would be brittle and crack easily.
Again water is added to help mix in the wood pulp and carry the mixture onto the next part of the manufacture process. At this stage it has consistency of thick porridge. More additives go into liquid sand cement and pulp to create a slurry that will make actual fibre cement product. The cylindrical SIDS have been lowered into troughs into which slurry is pumped.
Fibre cement slurry
source:https://www.youtube.com/watch?v=lpS6zhsLhmc
As the SIDS rotate slurry particles adhere to outer surface. Water drain through the mesh leaving a thin fibre cement fill on the sieve.
Fibre cement fill on the sieve
source:https://www.youtube.com/watch?v=lpS6zhsLhmc
The fils are picked up by felt belt running above the SIDS and the thickness of the product is built up like in laminate.
This is deposited to making drum with a circumference to dictate the length of product. Products are left stand for a while before moved into the autoclaves. Inside the autoclaves pressurized steam is used to cure the product for 9 hours at 170 degrees Celsius .
Fibre cement autoclaves
source:https://www.youtube.com/watch?v=lpS6zhsLhmc
The hole production process from raw materials to finishing the cement products takes 3 days
Lenghts of fibre cements boards
It is well understood that fiber length plays an important role in the properties of fiber cement. Below picture presents the impact of the percentage of fibers on fracture toughness for the resulting fiber cement for five different fiber lengths.
The effect of fiber length on fracture toughness
source:University of Idaho”TECHNOLOGY AND MARKET CONSIDERATIONS FOR FIBER CEMENT COMPOSITES”
Fracture toughness is an important parameter as it signifies the resistance of the fiber cement to fracture development and ultimately the failure of the product. As it is clear from this figure, longer fibers impart
higher fracture toughness to fiber cement.
Fibers with a length of 3.12mm clearly continue to exhibit higher strength over the range of 2-10 percent fiber content.
On the other hand, fiber length of 0.30mm provides virtually no improvement in fracture toughness over the range tested. It is believed that short fibers do not provide any significant bridging properties upon micro-crack development and generally act more as fillers.
Fibre cement cladding board strength
It is clear that addition of fibers to fiber cement imparts a number of attributes that are important to the application and serviceability of the composite.
It is noted that fibers that bridge the crack without slipping out or breaking slow or block crack development.
Fibers in fiber cement showing fiber bridging
source:University of Idaho”TECHNOLOGY AND MARKET CONSIDERATIONS FOR FIBER CEMENT COMPOSITES”
Fibre cement product attributes
- High fire resistance
- Durability
- Paint stability on finished product
- Resistant to impacts (high toughness values)
- Resistance to high winds
- Light weight
- Reduced waste on job site
- Capability for aesthetically pleasing products
- Resistant to ultraviolet light
- Good strength properties
- Nailable, sawable, cuts with woodworking tools
- Increasingly well accepted by architects and builders
Fibre cement applicattions:
- Facade
- Soffit
- Fascia
- Utility panel (tile backer, storage house siding)
- Decorative fence panels
- Patio Decking
- Light commercial construction panels
- Exterior cladding
- Fire retardant structures
- Swimming pool surroundings
- All types of display
- Reception desk
- Airline ticket counters
- Counters for restaurant, shops
- Decorative applications
- Modular building systems
Fibre cement meaning for UK
Fibre cement composites have gained an increasing foothold in United Kingdom market over the last twenty years. The fiber cement industry has experienced significant growth since 2002. Composites are poised to offer product replacement as well as new applications as we move into the next decade and beyond.
Fibre cement cladding is by far one of the most durable products on the market. When you use fiber cement siding for your house, then you are using a product that will withstand the elements for several years.
It is a product which is not flammable
When you poll the average homeowner about what events scare them the most, a fire at home is usually at or near the top of the list. That’s why fiber cement cladding is such a fantastic product to use for the exterior of the structure. 90% of the composition of this product comes from materials which are inflammable. Even in instances of extreme heat, this siding can hold strong. It has a Class 1(A) rating, the highest available and is mostly unaffected by direct flames and heat.
Fibre cement cladding boards structure
The texture of the piece makes it look like real wood, brick or stone. That means you can still enjoy the traditional look without sacrificing the many benefits that come with modern products.
Fibre cement low maintanace
The maintenance requirements for your new fiber cement siding are straightforward. You can spray down the structure with a low-pressure water source. Fiber cement cladding looks great with low-maintenance needs more than a decade after installation in almost any environment. When you choose fiber cement siding for your new home or for a remodeling project, then you are selecting a long-term solution that requires minimal maintenance. The estimated maximum service life for a non-back coated product from today’s manufacturers is typically 50 years.
More Articles:
Cedral Cladding and Frequently Asked Questions
Cedral cladding. Lap or Click?
How to install Cedral Click Cladding
How to install Cedral Lap Cladding
How to clean fibre cement cladding?
Weatherboard Touch Up Paint for Cedral
How much is Cedral cladding per square Metre?
Cedral Weatherboard. Timeless façade board?
*All the information provided in the content published on Insulationgo blog is for informational and educational purposes only. Insulationgo LTD makes every effort to ensure the accuracy and timeliness of the content, but we do not assume any responsibility for any errors or omissions.
The information presented on this blog should not be considered as professional advice or a substitute for consulting relevant experts. Before making any purchase decisions or taking action based on the information presented here, it is strongly recommended to contact the product manufacturer directly to verify the details and ensure its suitability for your specific needs.
By using this blog, you acknowledge and agree that Insulationgo LTD shall not be held liable for any damages, losses, or inconveniences arising from the use or reliance on the information provided herein. This limitation of liability applies to all users of the blog, including but not limited to visitors, readers, and subscribers.
Biography
1.iibcc.biz, Moslemi Al Professor Emeritus, University of Idaho”Technology and market considerations for fibre cement composites” November 5-7 , 2008 Madrid, accessed April 19, 2022
https://www.iibcc.biz/wp-content/uploads/2015/11/moslemi-technology-and-market.pdf
2.youtube.com “How it's made - James Hardie® fibre cement products” April 19, 2017, accessed April 19, 2022
https://www.youtube.com/watch?v=lpS6zhsLhmc
3.greengarageblog.org, Miller Brandon ”18 Pros and Cons of Fiber Cement Siding” June 5, 2019, accessed April 19, 2022
https://greengarageblog.org/18-pros-and-cons-of-fiber-cement-siding
4.sciencedirect.com, Fuente Elena “Hatschek process as a way to valorize agricultural wastes” 2017, accessed April 19, 2022
https://www.sciencedirect.com/topics/engineering/hatschek-process